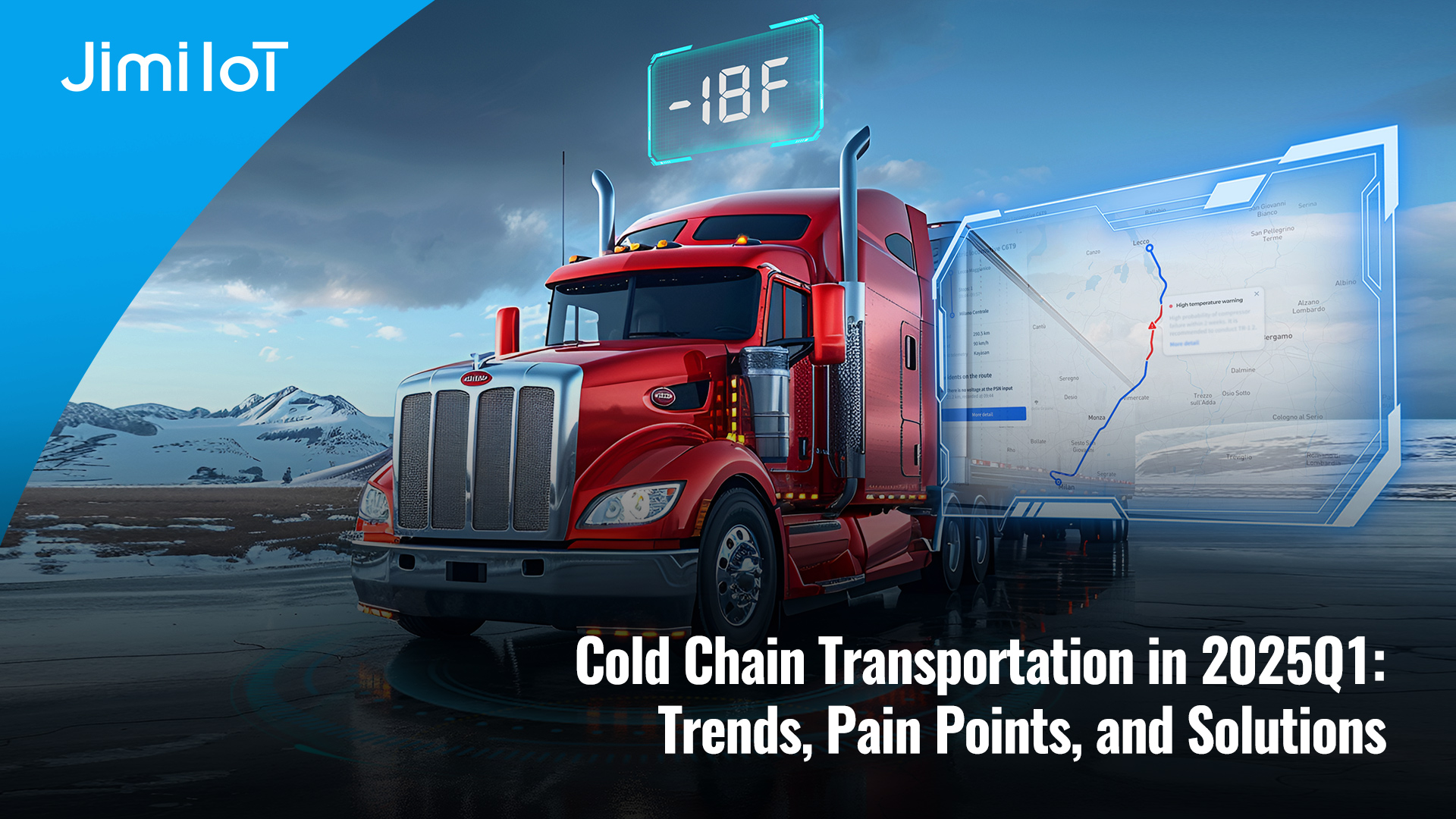
The cold chain transportation industry is set for significant transformations in 2025. As demand for perishable products like food, vaccines, and temperature-sensitive chemicals rises, cold chain transportation is becoming more critical than ever. At the same time, customers in logistics, pharmaceuticals, food distribution, and agriculture face new challenges: rising costs, tougher regulations, and increasingly complex delivery requirements.
To stay competitive, companies must both understand these emerging industry trends and address the key pain points that their customers experience. This article explores the latest cold chain trends, pinpoints common customer challenges, and offers practical solutions – including examples of innovative technologies like the LL309 Temperature and Humidity Monitoring Tracker – to ensure products remain safe, compliant, and cost-effective throughout transit.
Industry Trends Shaping the Cold Chain
Several major trends are defining the cold chain sector today:
- Growing Demand and E-Commerce: Global consumption of frozen and refrigerated goods is rising due to population growth, higher living standards, and the expansion of online grocery and meal-kit services. Consumers want faster home delivery of fresh food and pharma products, pushing logistics providers to expand capacity. This trend drives demand for more refrigerated trucks, containers, and urban cold storage facilities close to population centers.
- Advanced IoT and Connectivity: Technology adoption is accelerating. Internet of Things (IoT) devices with built‑in sensors and real-time connectivity are becoming standard tools. These devices monitor temperature, humidity, and location continuously during transit. With more shipments tracked by connected sensors, companies can detect problems immediately and optimize their routes and inventory. For example, new asset trackers now combine GPS tracking with environmental sensors, ensuring uninterrupted visibility into cargo conditions.
- Data Analytics and Artificial Intelligence: The explosion of data from connected devices is transforming decision-making. Predictive analytics and AI tools are being used to forecast demand, optimize delivery routes, and anticipate equipment maintenance. Logistics providers are investing in software platforms that analyze past temperature excursions and delays to reduce waste. This shift toward “smart logistics” helps companies plan for disruptions and improve on-time delivery for sensitive goods.
- Automation and Robotics: Warehouses and cold storage facilities are increasingly automated to boost efficiency. Robotics, automated storage/retrieval systems, and digital conveyor systems reduce manual handling of goods and minimize human error. Automation helps speed up loading/unloading and maintains consistent temperature control throughout the facility. It also addresses labor shortages in aging workforces while lowering operational costs.
- Regulatory Pressure and Food Safety: Governments and international agencies have tightened regulations on cold chain compliance. Pharmaceutical products and high-value foods often require detailed documentation of temperature logs for each shipment. Compliance standards (such as FDA guidelines, EU GDP, and WHO Good Distribution Practices) demand rigorous traceability. These regulations ensure safety but also create burdens for companies to collect, store, and report data at every step.
- Sustainability and Energy Efficiency: Cold chain logistics is energy-intensive, accounting for a large carbon footprint. Customers and regulators are demanding greener practices. In response, companies are investing in energy-efficient refrigeration, using eco-friendly refrigerants, and exploring renewable energy sources (like solar panels on warehouses or electric refrigerated trucks). Reducing waste through better temperature control also aligns with sustainability goals by cutting down spoiled goods.
These trends set a backdrop for the cold chain industry. But amid this progress, customers face persistent pain points that can threaten margins, compliance, and customer trust. The next section outlines the most pressing challenges encountered by cold chain stakeholders today.
Key Customer Pain Points in Cold Chain Transportation 2025
Cold chain customers – including pharmaceutical shippers, food suppliers, and logistics firms – repeatedly report several critical pain points:
- Maintaining Precise Environmental Conditions: The most fundamental challenge is keeping products within required temperature and humidity ranges throughout the journey. Even short deviations can spoil vaccines, food, or chemicals, leading to costly losses or health risks. Temperature breaches can occur during loading, unloading, or due to equipment failure. Customers need confidence that each shipment’s internal environment remains stable from origin to destination.
- Lack of Real-Time Visibility: Many cold chain operations still rely on manual logs or infrequent checks, meaning managers often learn about problems only after the fact. Without real-time tracking, shipments can become “black boxes” in transit. This visibility gap makes it hard to respond to issues like route delays, equipment malfunctions, or theft in time. Customers increasingly demand continuous visibility so they can take corrective action immediately when conditions deviate.
- Regulatory Compliance and Documentation: Heavily regulated sectors like pharmaceuticals require exhaustive record-keeping. Any gap in temperature logs or chain-of-custody documentation can result in non-compliance penalties or rejected shipments. Manual data recording is error-prone and labor-intensive. Companies must find reliable ways to generate tamper-proof audit trails that satisfy inspectors and meet complex standards across different regions.
- Infrastructure and Capacity Constraints: In many regions, the cold storage and transport infrastructure is underdeveloped. Rapid urbanization has outpaced the construction of warehouses and cooling facilities near consumption centers. As demand rises, companies face challenges finding or building enough refrigerated space and vehicles. Limited parking, scarcity of dedicated freight hubs, and shortage of trained drivers further stress the network. Customers encounter bottlenecks when there simply isn’t enough cold chain capacity to meet demand.
- Rising Costs and Energy Efficiency: Cold chain logistics is inherently expensive. Specialized refrigerated trucks, energy-hungry freezers, and temperature-control packaging all cost more than standard shipping. Customers feel pressure on thin profit margins. Moreover, fluctuations in energy prices directly impact operating costs. Maintaining profitability requires not only controlling costs but also extracting value (for example, by reducing spoilage). Efficiency is critical, from route planning to minimizing idle time for refrigerated containers.
- Complex Last-Mile Delivery: The “last mile” – the final leg from distribution hub to end customer – is especially complicated for cold chain. Deliveries must often navigate dense urban traffic or remote rural areas, all while keeping goods cold. Coordinating last-mile deliveries involves tight delivery windows, varying handling requirements (home delivery vs. store drop-off), and potential additional handoffs. Each transfer point is a risk for temperature excursion. Customers in food and healthcare demand very precise last-mile service quality, and any lapse can damage reputation or result in regulatory issues.
- Data Overload and System Integration: While more sensors and systems exist, companies often struggle to make sense of the data deluge. Multiple monitoring devices, telematics systems, and order management platforms can create silos of information. Integrating these systems so that data flows smoothly (for example, from a truck’s temperature sensor into a central supply chain dashboard) is challenging. Without unified data, it’s hard for customers to get actionable insights, conduct predictive analytics, or share information seamlessly with partners and regulators.
- Sustainability and Environmental Concerns: Finally, customers are increasingly conscious of the environmental impact of their supply chains. Consumers and retailers are demanding transparency about carbon footprint and waste. Some companies feel pressured to adopt greener cold chain practices but are unsure where to start. They worry about balancing sustainability initiatives (like switching to solar power or eco refrigerants) with the costs and reliability of these new solutions.
Together, these pain points can lead to higher rates of product loss, frustrated clients, regulatory fines, and damage to brand reputation. The rest of this article outlines practical strategies and technologies that address these challenges head-on, helping cold chain customers enhance reliability and efficiency.
Practical Solutions and Innovations
To overcome the outlined challenges, cold chain operators are turning to a combination of proven best practices and emerging technologies. Below are several actionable solutions:
IoT Tracking and Real-Time Monitoring
Implementing connected monitoring devices is one of the most direct ways to address visibility and environmental control issues. Modern IoT trackers and sensors can continuously record internal conditions and location data, alerting managers immediately if anything goes wrong.
For example, devices like the LL309 Temperature and Humidity Monitoring Tracker integrate multiple capabilities in one asset. The LL309 is a cellular (4G) tracker that provides real-time GPS location and simultaneously measures internal temperature and humidity. If readings drift outside preset limits, it sends instant alerts via the mobile network. Crucially, it also stores thousands of data records onboard in case of temporary network outages, ensuring a complete audit trail. By deploying such multi-sensor trackers on pallets, containers, or vehicles, companies gain visibility end-to-end. They can intervene quickly to adjust conditions or reroute shipments before spoilage occurs. Moreover, real-time data from trackers enables automated compliance reporting and reduces reliance on manual logbooks.
Other practical steps include placing fixed IoT sensors in cold storage facilities and trucks. These sensors link to cloud platforms or Transportation Management Systems (TMS), making environmental data accessible on dashboards. With mobile apps or web interfaces, operators and customers alike can monitor each shipment’s health from anywhere. This transparency not only prevents losses but also builds trust. For instance, a pharmaceutical shipper can show regulators a live feed of vaccine temperature data, demonstrating adherence to safety protocols.
Data Analytics and Predictive Management
Collecting data is only half the battle; making sense of it is equally important. Advanced analytics tools can turn historical temperature logs and delivery records into actionable intelligence. By analyzing patterns, companies can predict when problems are likely to occur and optimize operations accordingly.
For example, predictive analytics can forecast temperature excursions by correlating outside weather forecasts with vehicle performance data. If a particular route in summer tends to cause truck refrigeration units to work overtime, planners can adjust by choosing alternate routes, scheduling more frequent maintenance, or adding extra insulation on that leg. Airlines or 3PLs might use machine learning algorithms to identify which shipments are at highest risk of delay or spoilage, allowing them to prioritize monitoring for those loads.
Similarly, integrating data from sensors with warehouse management systems supports dynamic inventory control. If an IoT tracker indicates a cold room is trending toward higher temperatures, the system can automatically reroute goods to alternate storage or increase cooling power. Over time, companies also mine data to improve packaging choices: for instance, analyzing which types of pallets or gel packs maintained steady temperature longest under certain conditions. These insights allow cold chain operators to refine every aspect of their process.
Automation and Process Optimization
Automation is a key trend in modern cold chain logistics. Automating manual processes reduces human error and increases efficiency. For instance, automated doors, temperature-controlled loading bays, and conveyor systems in refrigerated warehouses ensure that doors stay closed and temperatures remain stable during transfers.
On the software side, Transportation Management Systems (TMS) can automate alert workflows. When a temperature sensor sends an alert, the system can automatically notify the relevant personnel (drivers, fleet managers, or customers) by text, email, or app notification. This instant communication minimizes delays in response. Other systems can automate compliance paperwork: for example, generating time-stamped reports of temperature logs whenever a shipment is received, simplifying audit preparation.
At the last-mile level, some companies are experimenting with automated guided vehicles (AGVs) or drones for delivery of small cold items in cities, reducing transit time and exposure to heat. While still emerging, such innovations point toward a future where consistency and speed improve along the entire chain.
Cost Control and Efficiency Measures
Given the high costs of cold logistics, finding efficiencies pays off quickly. Fuel economy can be improved through careful routing and speed control. For instance, telematics systems can optimize truck speeds and use real-time traffic data to minimize idling time in traffic or at loading docks – both of which save fuel and reduce fluctuations in internal temperature.
Energy efficiency in facilities is another area for savings. Upgrading to LED lighting, variable-speed compressors, and better insulation can dramatically cut electricity use in warehouses. Some companies add rooftop solar panels or engage with green energy programs to offset costs and carbon output. Packaging innovations also help control temperature passively: high-performance insulated blankets, vacuum panels, or phase-change gel packs can maintain target temperatures longer during brief power losses or transfers.
From an operational perspective, cross-training staff on cold chain protocols ensures fewer mistakes. Simple steps like minimizing door openings, scheduling frequent equipment checks, and following strict loading procedures can have outsized impacts on consistency and waste reduction.
Conclusion
The cold chain transportation industry is at a pivotal point, driven by escalating demand for fresh and temperature-sensitive goods, rapid technological advances, and stricter regulations. For logistics firms, pharmaceutical companies, food suppliers, and agricultural exporters alike, the bottom line is clear: addressing customer pain points in the cold chain is critical to preserving product value and competitiveness. By adopting a combination of smart technologies (such as IoT sensors and trackers), data-driven practices, automation, and efficiency measures, companies can turn those pain points into opportunities for innovation.
For example, deploying advanced tracking devices – from cellular trackers to Bluetooth sensors – provides the real-time visibility needed to prevent spoilage and streamline compliance. Investing in analytics and modern management systems helps anticipate problems before they become emergencies. And through strategic infrastructure planning and sustainability initiatives, businesses can manage costs and align with global environmental goals.
In short, the industry’s trends and challenges go hand in hand: every technological trend offers a way to solve a pressing challenge. By staying informed about emerging solutions and incorporating them thoughtfully (such as using examples like the LL309 monitoring tracker to illustrate the power of IoT), cold chain operators can meet customer needs head-on. The result will be more resilient, efficient, and trustworthy cold supply chains – a win-win for businesses and their customers in an increasingly temperature-driven world.
Why JimiIoT
JimiIoT is a global leader in innovative IoT solutions. We provide cutting-edge hardware and software tailored to enhance efficiency and connectivity. Our range of products includes advanced GPS tracking devices, asset management solutions, smart vehicle dashcams, and telematics platforms. With a focus on technological excellence and customer satisfaction, we empower businesses to optimize operations and gain valuable insights from data-driven analytics. Trust JimiIoT to drive positive change and unlock growth opportunities in the digital age.
If you would like more details, please visit Facebook, LinkedIn, INS, and Twitter pages for further information.